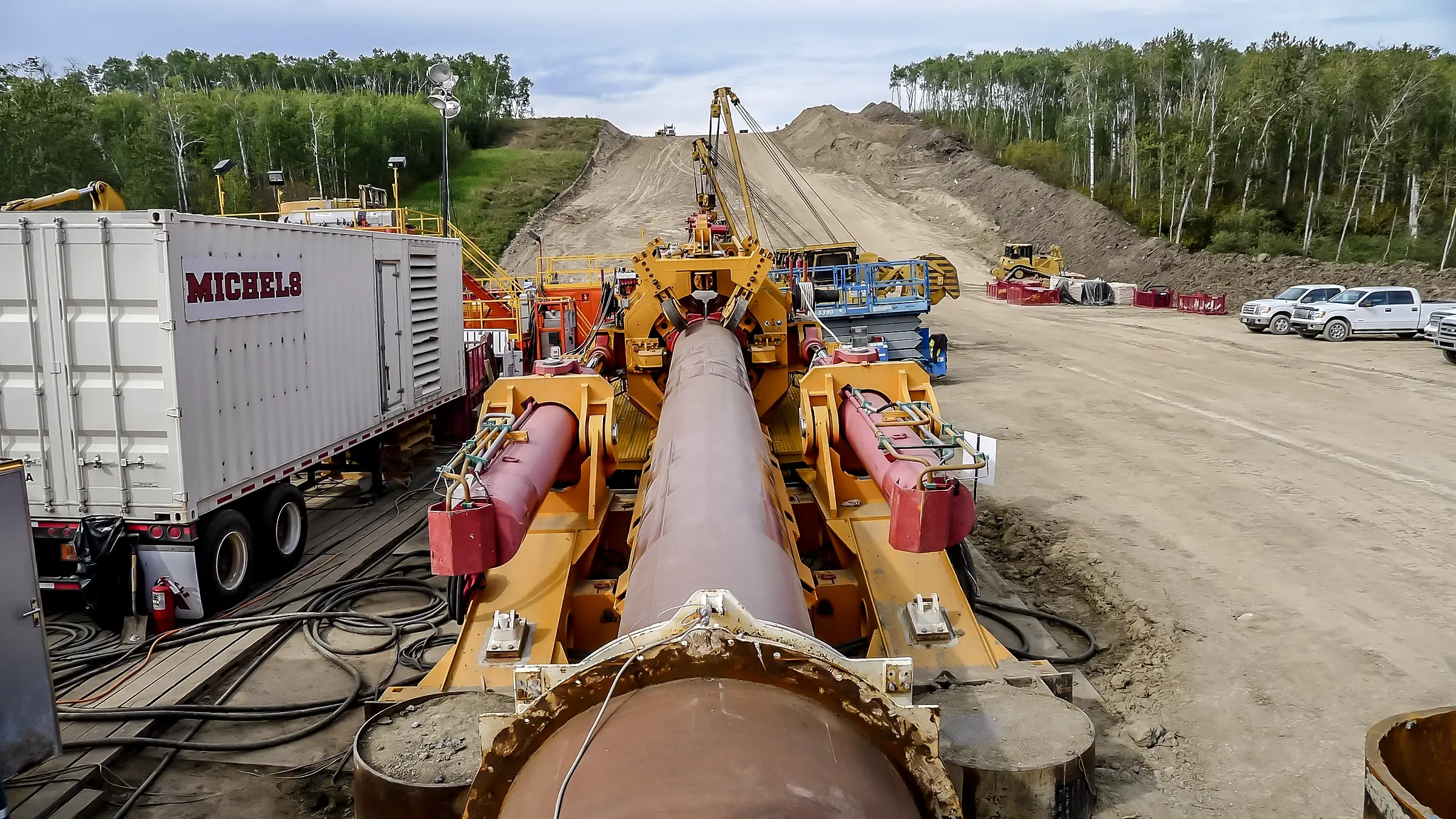
The Project
Twenty kilometres northeast of the town of Bonnyville, Alberta, a steel pipeline needed to be installed underneath the Beaver River. The particular crossing was part of the greater Inter Pipeline Cold Lake and Polaris expansion program, which was a 560 kilometre oil pipeline project from Edmonton to Fort McMurray, Alberta. Originally, Beaver River had intended to be crossed via horizontal directional drilling (HDD).
HDD vs. Direct Pipe
We’re going to get technical for a moment and then go back to the Beaver River Crossing case study. So, the conventional trenchless method of HDD often requires deep installations to facilitate construction in subsurface conditions that can withstand anticipated annular pressures. Drilling through adequate geotechnical formations at specified depths during an HDD installation helps mitigate the potential of an inadvertent release of drilling fluid that might otherwise occur. To maintain operations within a desired geotechnical formation capable of handling anticipated annular pressures, HDD installations are designed with a parabolic arc that extends the overall length of the installation at the same time it ensures that entry and exit angles are kept relatively small and maximum bending stresses on the pipe string are not exceeded.
Conversely, the Direct Pipe® installation method is capable of operating within various types of geotechnical formations at much shallower depths with little risk of an inadvertent fluid release. Since the annular space is continuously supported during a Direct Pipe® installation and minimal static pressure is exerted on the earthen wall, the chances of an inadvertent fluid release are significantly reduced. Therefore, with less of an obligation to account for geotechnical formation, depth, and associated annular pressure in design, Direct Pipe® installations can be designed to accommodate a shorter crossing than HDD, especially where inadvertent fluid loss or risk of encountering worse conditions at greater depth is of primary concern. A shorter crossing can prevent damage to a product pipe, lessen inadvertent fluid release, save material and solve logistical challenges.
How to Determine the Best Approach for Beaver River
Okay, back to our case study. The team was poised to make an informed design decision; Rangeland Conservation Service (RCS) Ltd., an environmental and geotechnical services group from Airdrie, Alberta, was contracted to perform an initial geotechnical and feasibility report for the given crossing. The field program was conducted between November 7th and 10th, 2011, and consisted of drilling two boreholes, 40 meters in depth, one on each side of the river (Figure 1).
Potential Obstacles Revealed in the Design Report
The preliminary design report summarized the horizontal directional drilling (HDD) crossing as feasible from a geotechnical perspective, however, had the following reservations. Due to soil conditions encountered, an identified “no drill zone” was outlined because of the high chance of an inadvertent release of annular pressure underneath the river. The no drill zone profile is shown on Figure 2. It was further stated that all proposed HDD paths should be maintained outside of the zone. In order to meet the depth of cover required, RCS also specified preliminary entry and exit angles for the drill to be a relatively steep 18 degrees.
Detailed Design A Year in the Making
Michels and its partners spent about a year working on preliminary design. Direct Pipe was selected for the project to mitigate geotechnical and routing challenges as well as specific environmental and cultural sensitivities associated with the watershed. The area’s geology included sand, clay, clay shale, boulders, shells and wood.
Upon reviewing the given feasibility and logistical concerns of crossing the Beaver River with HDD, other trenchless approaches were sought after to lessen the challenges that were going to be faced with the particular crossing. Direct Pipe®, although new to the North American market, and entirely never utilized in Canada, seemed to be a feasible option.
Customized Solutions for the Project
Once the opportunity arose for the first appearance installation to be conducted, Michels Canada utilized a 42-inch machine from Herrenknecht, a tunnel-boring machine and mining equipment manufacturer, specifically designed for the Beaver River operation. Unlike the design of its predecessor, this Direct Pipe® installation would be carried out with an entry angle of only 4 degrees and an exit angle of 8 degrees (keeping in mind that Direct Pipe® equipment is only needed on entry side). The shallow entry angles would then furthermore allow the crossing to be conducted with five metres of overburden underneath the river bed, and as shallow as 4.6 meters in some areas, as opposed to approximately 12 metres minimum as specified with HDD (Figure 3).
Achievements
- Reached the reception pit after just 13 days of drilling
- On their best day, crews reached up to 86 metres of pipeline installation
- Use of Direct Pipe alleviated seemingly challenging and lengthy additional HDD designs, saving saves time and money for all parties involved.
- Michels Canada use of Direct Pipe in Beaver Creek project was first time this approach was successfully used in Canada