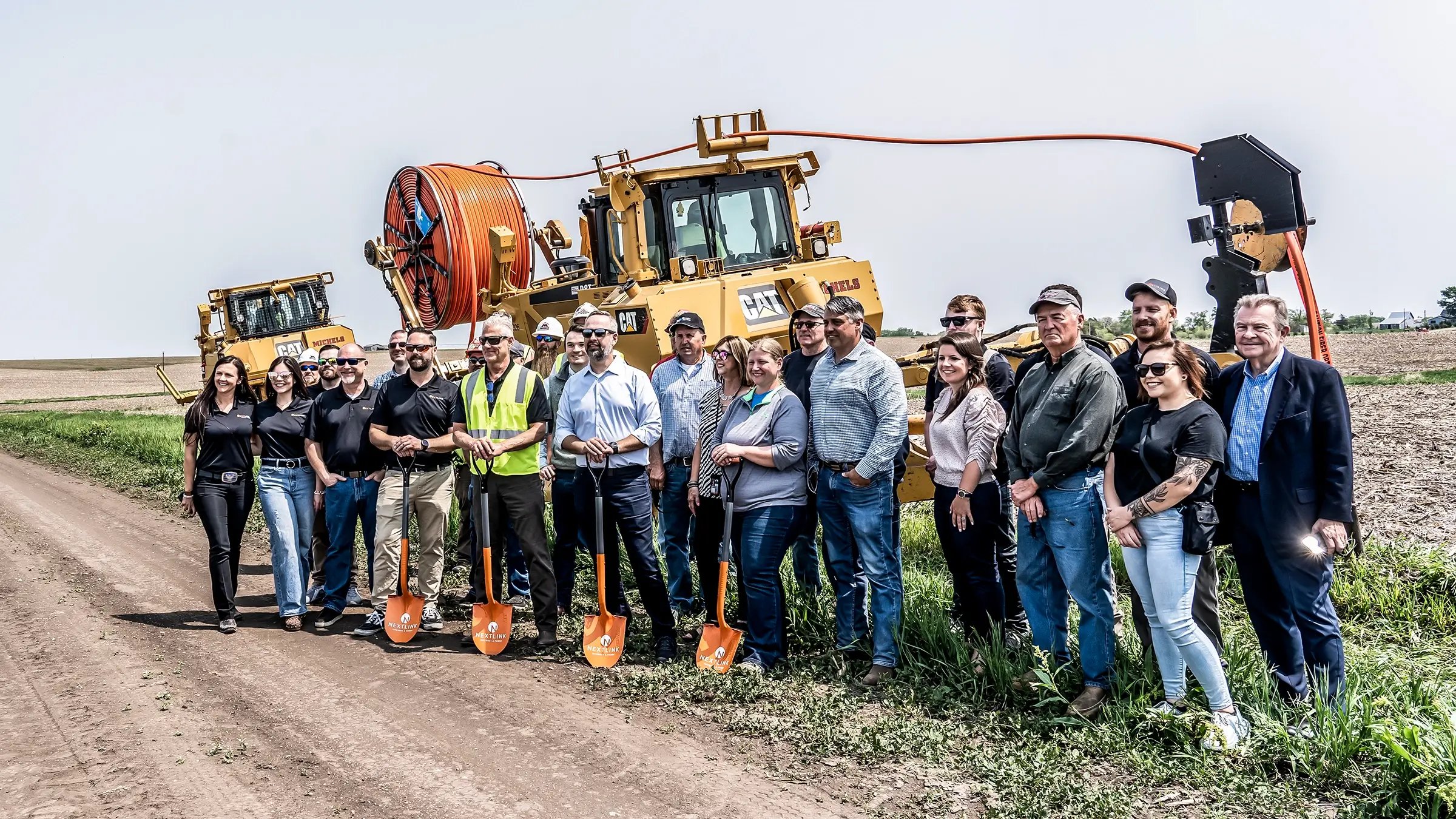
News
Learn What's New
Most of the work we do takes place underground—in the tunnels we mine, the utility lines we install, and the foundations we build. The success of our projects is most often measured in reliability, effectiveness and technical test results, rather than something more visual.
The stories of our successes and values at work are much easier to uncover. Search our news to learn more about Michels. You are likely to find We Do That … & More.
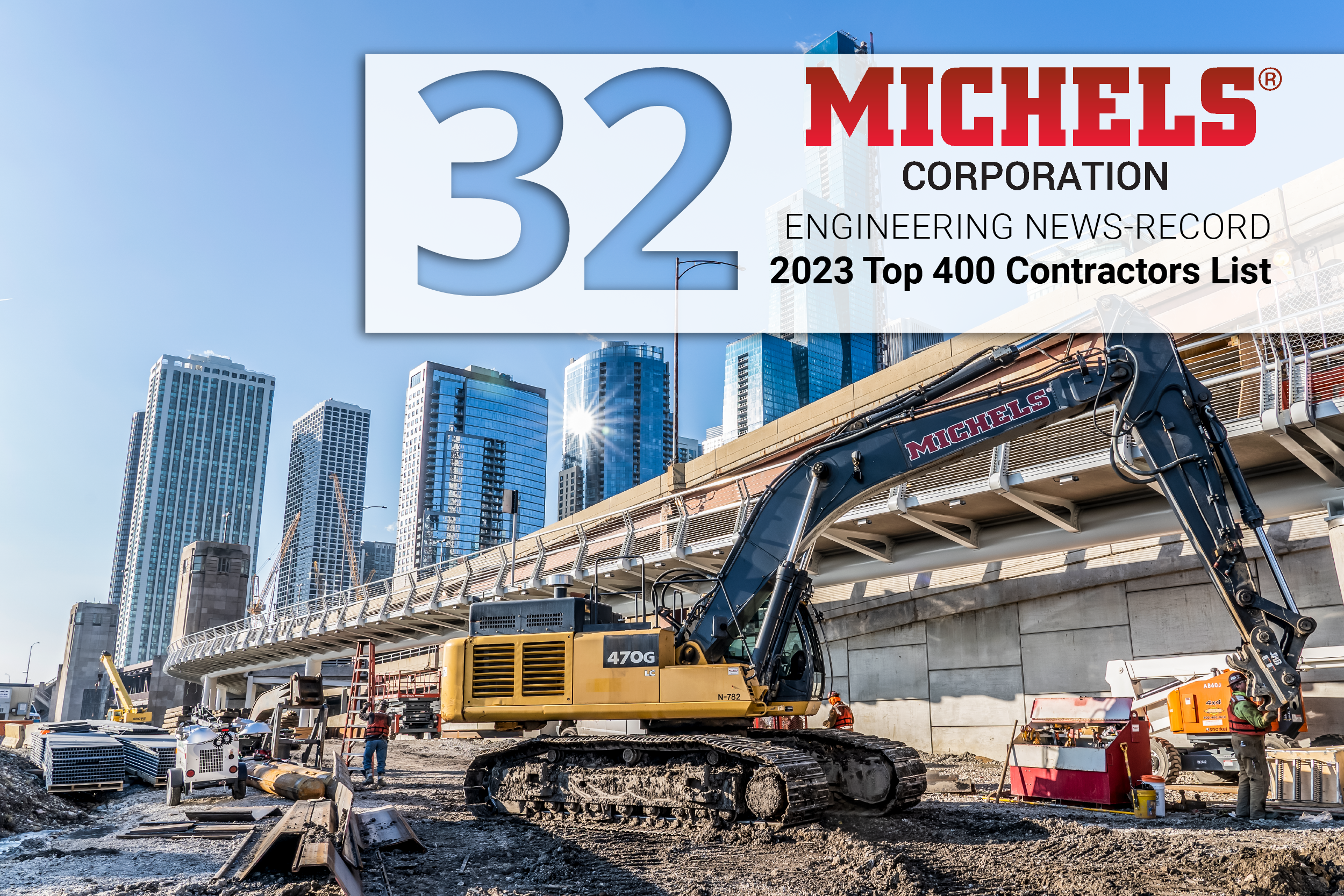
Accomplishments
Michels ranks 32nd on ENR Top 400 List
Michels is proud to be ranked as the 32nd largest contractor on the 2023 Engineering News-Record Top 400 Contractors List. As a specialty contractor focused on supporting our country’s energy and infrastructure industries, Michels is honored to maintain our positions as 6th among Petroleum Contractors and 8th among Power Contractors. Maintaining a spot among the...Search All News
